Single tube spiral weighing feeder
Performance Characteristics

Exquisite structural design
The biggest feature is that the measurement and feeding are carried out simultaneously, which can be completed by only one screw. Convenient transportation, no space occupation, and cost savings.

Steady current technology
Adopting industry-leading stable flow technology, it fully ensures smooth material transportation, prevents arching, prevents material blockage, and also guarantees stable accuracy in actual use.

User friendly and easy to operate
The operating interface of this device is very intuitive, and users can manually input parameters. Daily maintenance is also simple and easy to operate.

User friendly and easy to operate
The instrument equipped with the spiral scale has zero point automatic tracking function, and the relevant weighing data can be protected in a timely manner. The RS-485 communication interface can also be configured and centrally controlled by the industrial computer.
Product Composition

Weighing Body
Measurement and feeding are completed simultaneously in a single tube. Precision manufacturing, long-term use without deformation. Sealed structure to avoid material waste.
Control Cabinet
our control cabinets come with power outage protection - they'll automatically pick up right where they left off when power returns. You can remotely monitor real-time data through the system . Plus, we've got massive storage capacity - check daily or monthly data anytime you need. Makes management way easier.
digital sensors
Our load cells feature digital sensing tech with built-in noise resistance and lightning-fast readings. The auto-range calibration cuts measurement errors big time. IP65-rated protection keeps them running smooth even in nasty conditions.
Speed sensor
Speed sensors with cast aluminum armor thrive outdoors – rain or shine. Brushless DC pulse generator design = zero upkeep.
Working Principle
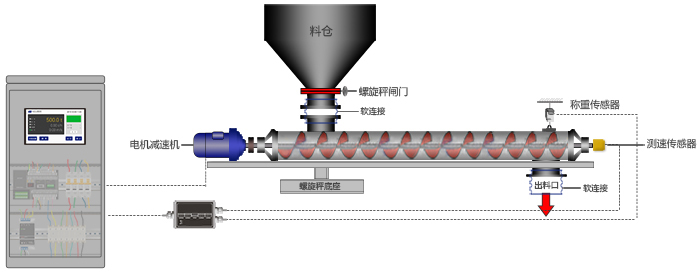
The material is transported by a screw conveyor from the feeding port to the measuring cutter connected below, and the fully weighed weight of the measuring screw is sent to the controller through three tension sensors installed on the measuring cutter as a voltage signal proportional to the weighing load, along with the preset cutter speed data (when measuring with double pipes, the measuring cutter runs at a constant speed to advance the material, that is, the speed signal is the design value of the measuring cutter).
At this time, the weight and speed signals are calculated to obtain the instantaneous flow rate and cumulative weight value. The control system of the spiral quantitative feeding scale compares the actual flow rate signal with the set flow rate signal, and outputs the control signal to the frequency converter through PID adjustment. The speed of the feeding cutter is dynamically adjusted to achieve quantitative feeding.